Requirements for scratch-resistant of automotive interiors
In recent years, as people’s attention to air quality in cars has gradually increased, the problem of air pollution in cars has become increasingly prominent. The main source of air pollution in cars lies in interior materials such as plastic. Therefore, solving the problem of air pollution caused by interior materials has become one of the current problems that need to be solved urgently.
Among automotive plastics, polypropylene (PP) has been widely used in automobiles due to its low density, high-cost performance, excellent heat resistance, rigidity, material modification, easy processing, molding, and recycling, and has become an automotive plastic. The variety with the largest dosage and the fastest development rate. However, the scratch resistant of PP is significantly poor, which is key to automotive interior application components such as instrument panels, consoles, and door panels. Therefore,anti scratch resistant coating for cars improving the anti scratch resistant of PP has become one of the current problems that need to be solved.
The characteristics of ordinary anti PP scratch resistant agent can easily cause the content of volatile organic compounds in PP to be too high, which cannot meet the performance requirements of automobile interiors such as odor and atomization. In addition, since the previous amide slip agents are low molecular weight substances, when they migrate to the surface of the material, they will not only cause problems such as stickiness, blooming, and whitening on the surface of the product, but will also affect the odor and emission characteristics of the material, resulting in The content of volatile organic compounds is too high, seriously polluting the air in the car, and becoming an “invisible killer” affecting the health of drivers and passengers.
In addition to focusing on the scratch resistant and odor-emitting properties of PP, it is also necessary to consider the impact of other factors on automotive interior components. For example, the color and gloss of automotive interior components are also of the key factors affecting their aesthetics and performance. Interior parts of different colors will give people different visual feelings, and may also affect the emotional and psychological state of the drivers and passengers. Therefore, when choosing the color of interior components, coordination and comfort with the overall car interior design need to be taken into consideration. In addition, gloss is also one of the important factors affecting the aesthetics of interior parts. A high-gloss interior component can give drivers and passengers a more luxurious and comfortable visual experience, while also improving the overall grade and quality of the car.
In order to solve the anti scratch resistant problem of PP, some automobile manufacturers and plastic suppliers have begun to explore the use of high molecular weight substances as alternatives to PP scratch resistant agent. High molecular weight substances have higher scratch-resistant and lower volatile organic content, so their use in automotive interior components can improve their overall performance and safety. However,anti scratch resistant coating for cars the cost of high molecular weight substances is relatively high, and their melting point and fluidity also need to be paid attention to during processing.
Another approach is to use nanotechnology to improve the scratch resistant and odor-emitting properties of PP. Nanotechnology is an emerging technology that breaks down materials into smaller units – nanometer-sized particles. These nanoparticles have very high surface energy and activity, which can effectively improve the scratch resistant and odor-emission performance of PP. By applying nanotechnology to PP, the anti scratch resistant of PP can be effectively improved and its volatile organic content can be reduced. This technology can not only improve the aesthetics and performance of automotive interior components but also improve the overall grade and quality of the vehicle.
Xiangxi PP anti PP scratch resistant agent fully demonstrates that the anti scratch resistance requirements of automobile interiors are one of the key factors to ensure the aesthetics and performance of automobile interior parts. By improving the scratch resistant and odor-dispersion properties of PP plastics, the quality and safety of automotive interior components can be effectively improved, providing drivers and passengers with a healthier and more comfortable interior environment. At the same time, the application of nanotechnology also provides safer and more environmentally friendly choices for automotive interior materials and will become one of the development directions of automotive interior materials in the future.
Product Description of Xiangxi PP Scratch Resistant Agent DX8502
Xiangxi PP scratch-resistant agent DX8502 is a modifier based on a polypropylene (PP) matrix. It uses advanced radiation cross-linking grafting alkoxysilane technology and then extends the macromolecular silicone through hydrolysis and condensation reaction to form A scratch-resistant agent with a molecular weight of over 3 million. It is suitable for all plastic, rubber, and elastomer systems, and can significantly improve the scratch resistance, lubrication performance, and release performance of these materials while improving the wear resistance and scratch resistance of the products. In addition, it increases the surface finish of the material, further enhancing processability and feel.
The application of scratch-resistant agent DX8502 in automotive interior materials is of great significance. In recent years, the problem of air pollution in cars has become increasingly prominent. One of the main sources of pollution in car air quality is volatile organic compounds (VOCs) released by interior materials such as plastics. These compounds not only have a negative impact on human health but also have an impact on the car’s riding environment and driving experience. Therefore, improving the environmental performance and human-friendliness of automobile interior materials is one of the urgent problems in the current automobile industry that needs to be solved.
Anti-scratch agent DX8502 provides a new solution for automotive interior materials by improving the scratch resistance of PP materials and reducing VOC content. First of all, it can significantly improve the scratch resistance of PP materials, making automotive interior parts less likely to be scratched or worn, thus improving the service life and appearance quality of the parts. Secondly, the low volatility characteristics of the PP scratch resistant agent DX8502 enable the VOC content in PP materials to be effectively controlled, thereby reducing the risk of air pollution in the car. This has a positive effect on improving the physical health of drivers and passengers and also helps improve the driving experience and riding comfort of the car.
In addition to the improvement of environmental performance and scratch resistance, scratch-resistant agent DX8502 also has excellent processing properties. During the processing of PP materials, the scratch-resistant agent DX8502 can maintain stable processing performance and will not have a negative impact on the melting state, fluidity, and thermal stability of PP materials. This allows PP materials to maintain stable performance during processing, thereby reducing production costs and scrap rates and improving production efficiency.
In addition, the scratch-resistant agent DX8502 also has good dispersion and compatibility and can be well-compatible with other additives in PP materials without causing aggregation, precipitation, or delamination. This allows the scratch-resistant agent DX8502 to be evenly distributed in the PP material, making the various performance indicators of the PP material more stable and reliable.
The molecular structure of Xiangxi PP scratch-resistant agent DX8502 enables it to achieve high compatibility in the PP matrix. This compatibility gives the PP material excellent processing performance and thermal stability, while forming a uniform distribution without precipitation on the surface of the material. This uniform distribution effectively improves the surface quality of PP materials, allowing them to exhibit better durability and aesthetics in various applications.
Anti-scratch agent DX8502 has excellent high temperature resistance. Even in high-temperature environments, there will be no stickiness or yellowing, thus ensuring the aesthetics and performance of interior materials. This property is crucial for automotive interior materials, which face high temperature and UV rays when cars are exposed to the sun for long periods of time.
In addition to high temperature resistance, the scratch-resistant agent DX8502 also has the properties of low VOC, precipitation resistance and stress whitening reduction. These characteristics make it not only comply with the strict environmental protection and safety requirements of automobile OEMs, but also comply with the pursuit of health, environmental protection and sustainable development of modern automobile interior materials.
Anti-scratch agent DX8502 also has excellent external and internal lubrication functions. External lubrication can significantly improve the processing performance of PP materials, increase its fluidity, reduce equipment wear, increase the discharging speed and reduce product deformation. At the same time, it can also form a uniform lubrication layer on the material surface, significantly reducing the surface friction coefficient and improving wear resistance. This property is very important for automotive interior materials, which need to have excellent sliding properties and wear resistance to maintain a good feel and service life.
In addition to external lubrication function, anti-scratch agent DX8502 also has internal lubrication function. It can improve the toughness and ductility of PP materials, thereby increasing the impact strength and tensile strength of the material. This allows the PP material to exhibit good fluidity during the extrusion molding process and produce products with smooth surfaces and no defects. In addition, the dispersion of the PP scratch resistant agent DX8502 enables it to form a uniform lubricating layer on the surface of the PP material, significantly improving the surface quality of the material.
Xiangxi PP scratch-resistant agent DX8502 is a high-performance, environmentally friendly scratch-resistant agent with excellent scratch resistance, processing performance and environmental protection performance. It provides a new solution for automotive interior materials and is an ideal choice for the development of future automotive interior materials.
Materialized data
model | DX8502 |
Chemical structure | PP hybrid silicone |
Appearance | white particles |
Melting index: g/10min/230℃ | 10.0﹣12.0 |
Density g/cm³ | 0.87-0.90 |
Moisture % | ≤0.2 |
Active ingredient % | 50 |
Chemical composition information
Chemical category |
mixture | ||
physical state |
Granular | ||
color |
White | ||
The main purpose |
General plastics, engineering plastics, elastomers and rubber | ||
Ingredients |
Chemical name | CAS number | %(W/W) |
polypropylene | 9003-07-0 | 30-40 | |
Silicone Rubber | 63394-02-5 | 45-50 | |
fumed silica | 112945-52-5 | 15-20 | |
Vinyl MQ Silicone Rubber | 68988-89-6 | 5-10 |
Physical and chemical properties
Material form/color | White particle |
odor | Odorless |
PH value | not applicable |
Moisture | 0.20% following |
proportion | 0.87-0.90 g/cm3 |
hardness | 99±1° |
Melt Index | 10.0–12.0 g/ 10 min |
Silicon content | 50±2% |
Decomposition temperature | No valid data |
Auto-ignition temperature | No valid data |
Explosion limit | No valid data |
Solubility in water | Insoluble in water |
Solubility in fats and oils | No valid data |
Vapor Pressure | No valid data |
Comparison of the application characteristics of different types of scratch-resistant agents:
Test items | DX8502 | Silicone anti-scratch agent | Ordinary silicone anti-scratch agent |
Product ingredients | Silicone with functional groups | Special silicone | Ordinary silicone |
Scratch resistance | +++ | ++ | + |
Scratch Resistant Durability | +++ | ++ | + |
Impact performance | ++ | + | ++ |
Resistant to stress whitening | ++ | + | — |
Haze surface | ++ | ++ | + |
Light and heat aging properties | ++ | ++ | + |
Odor, VOC performance | ++ | + | ++ |
Adding amount | Low | middle | high |
Application testing:
Test items | DX8502 | Silicone anti-scratch agent | Ordinary silicone anti-scratch agent |
Cross scratch ΔL(10N) | 0.46 | 1.37 | 2.54 |
Cross scratch ΔL(10N)(102℃,168h) | 0.51 | 0.98 | 1.93 |
Stress whitening ΔL | 0.21 | 1.03 | 1.46 |
Tensile strength (MPa) | 23.28 | 21.65 | 22.10 |
Bending strength (MPa) | 29.62 | 29.35 | 29.70 |
Elongation at break (%) | 63.58 | 68.35 | 64.10 |
Notched impact strength (23℃,kJ/m2) | 27.71 | 26.58 | 27.62 |
Surface precipitation | no | no | no |
Surface precipitation (thermal aging 168h) | no | no | no |
The Xiangsi DX8502 scratch-resistant agent is like the superhero for your PP resin. Picture it as a special agent with its own set of skills, thanks to those unique functional groups. These groups aren’t just there for show—they’re like anchors, securing themselves into the PP resin.
Now, when it comes to compatibility, this agent is basically the PP material’s best friend. They get along like a house on fire, and that’s a good thing. It easily blends in, making sure it’s evenly spread across the material’s surface. No favoritism here—every part gets its fair share.
And here’s where it gets really cool. You don’t need a ton of this agent to make a big impact. Even in small doses, it steps up and gives your PP materials top-notch scratch resistance. It’s like magic, but in the world of materials science.
In a nutshell, Xiangsi DX8502 is your go-to for enhancing PP materials. Scratch resistance? Nailed it. Compatibility? Like peanut butter and jelly. It’s all about making your PP resin the best version of itself, and this agent is the secret sauce.
Xiangsi DX8502 contains special functional groups that can be evenly enriched on the material surface, as shown below
Ordinary silicone and PP are incompatible, and the surface enrichment is uneven, as shown below
Let’s take a closer look at the scratch resistance of Acacia DX8502 in PP materials, specifically when blended with 20% talc and under the test standard PV3952 with a force of 10N.
Imagine your PP material, fortified by a dynamic combination of PP+20% talc – a strategic alliance that brings out the best of both worlds. Talc, known for its enhancing qualities, joins forces with PP to create a team that is not only powerful, but tailor-made for enhanced scratch resistance. Now, entering the realm of testing with the PV3952, a standard that passes material through a wringer with a force of 10N. It was like a battle of endurance, and the Acacia DX8502 stepped up as the unsung hero. Its unique composition, along with those special functional groups, creates a protective barrier on the PP+talcum powder blend.
What makes this scratch-resistant story compelling is the Acacia DX8502’s precision. This is not a one-size-fits-all solution; it is a tailor-made approach that ensures your PP material remains virtually unscathed, even when faced with 10N of force. This performance speaks volumes about the quality and effectiveness of this anti-scratch agent. Moreover, the even distribution of Acacia DX8502 on the surface of the material is like an art form. It doesn’t just sit there; It integrates seamlessly, ensuring every nook and cranny of the PP+talc mix is protected. This uniformity is key to achieving consistent scratch resistance throughout the material.
Essentially, what you get is a symphony of materials science – a harmonious blend of PP, Talc and Acacia DX8502, engineered to withstand the rigorous PV3952 test of 10N. This is more than just scratch resistance; this is a testament to the precision and effectiveness of this special agent in enhancing the durability of PP materials.
The advanced history of Xiangxichem DX8502PP anti-scratch solution is the story of the transformation of PP interior materials, especially in the face of challenges brought by light, heat and external forces. As temperatures rise, especially during the hot summer months, the fragility of PP interior materials becomes apparent. The inherent properties of the material, coupled with the fillers and additives introduced during the production process, can create a series of problems that not only affect the aesthetics, but also pose a potential threat to driving safety and comfort in the car.
odor:
During hot summer months, PP interior materials tend to release volatile organic compounds (VOCs) when exposed to high temperatures in enclosed spaces in cars. Not only does this pose potential health risks, it can also create unpleasant odors that impact the overall in-car experience. There was an urgent need for a solution to alleviate these issues, which paved the way for the launch of Xiangxichem DX8502PP.
Scratches and Scratches:
The inherent low hardness of PP material makes it prone to scratches and wear during daily use. Over time, dust accumulation can exacerbate this problem, causing visible white marks on the surface of the part. In addition to cosmetic aspects, these scratches can affect the overall look and feel of interior materials, reducing the aesthetics of the vehicle and driver comfort. Xiangxichem DX8502PP steps in as a transformative solution to enhance the scratch resistance of PP interior components and maintain their original appearance.
Stress Whitening:
External forces such as bending and impact during assembly can cause stress whitening in PP materials. Over time, these white marks will expand, not only affecting the appearance of the material but also compromising its mechanical properties. Factors such as elongation at break, strength, and resistance to stress cracking will be affected, posing a serious threat to the functionality and durability of the product. The emergence of Xiangxichem DX8502PP marks a turning point, solving the problem of stress whitening and enhancing the ability of PP materials to resist the harmful effects of external forces.
To address these challenges, the revolutionary Xiangxichem DX8502PP anti-scratch solution has emerged, changing the rules of the game. Its specialized functional groups establish a stronghold in the PP matrix, forming a protective barrier against scratches, scuffs and stress whitening. Xiangxichem DX8502PP’s compatibility with PP materials ensures seamless integration, allowing for uniform concentration on the material surface.
In addition, the role of Xiangxichem DX8502PP is not limited to appearance enhancement. By addressing the release of volatile organic compounds at high temperatures, it helps create a healthier interior environment. This solution not only improves scratch resistance but also protects the mechanical properties of the PP material, ensuring longevity and reliability.
In the intricate dance of materials science, Xiangxichem DX8502PP becomes the partner that takes PP interior materials to new heights. This isn’t just about addressing visible scratches; it’s about defending against unseen forces that threaten the integrity of the material. With Xiangxichem DX8502PP, driving is no longer just an experience, but a journey that enhances safety, comfort and lasting beauty.
In the ever-evolving landscape of automotive design, the demand for energy efficiency, environmental consciousness, comfort, aesthetics, and cost-effectiveness has become increasingly pronounced. Within this context, the improvement of Polypropylene (PP) interior materials has become a focal point in creating a car interior that is not only functional but also offers a heightened level of comfort and beauty.
Various modification methods have been explored to enhance the performance of PP interior materials, ranging from the addition of functional additives to strengthening modifications, toughening modifications, and alloying. Amid these strategies, XiangxichemDX8502 emerges as a pivotal player, leveraging the unique properties of silicone to elevate the performance of PP interior material parts.
The developmental journey of XiangxichemDX8502 spans several distinct stages, each marked by targeted research and development efforts aimed at addressing specific needs. Let’s explore the different phases of this innovative scratch-resistant agent’s product development.
Stage One: Pioneering Development (2019)
In response to the increasing demand for scratch-resistant agents tailored for automotive PP interior materials, Xiangxichem embarked on a developmental journey in 2019. Initial research and development revealed that incorporating mineral fillers, amides, and silicon-based additives into PP interior parts could effectively enhance scratch resistance. However, a challenge surfaced with small molecule scratch-resistant agents, as their inherent characteristics could lead to issues such as migration, stickiness, and yellowing during use. Moreover, these agents could impact the odor and emission characteristics of the material, potentially resulting in elevated levels of volatile organic compounds (VOCs) within the car interior. High VOC content could pose a serious threat to air quality, impacting the health of drivers and passengers.
This led to a pivotal shift in approach. By introducing polymeric silicone-based scratch-resistant agents to PP interior parts, Xiangxichem addressed not only the need for excellent scratch resistance but also mitigated the migration and stickiness issues associated with amides and mineral fillers. This marked the inception of a scratch-resistant agent for automotive PP interior materials in the early stages of research and development.
Despite facing limitations in experience and resources at this juncture, Xiangxichem’s product design goals extended beyond mere scratch resistance. The team began to actively consider the critical issue of low-odor safety for automotive interior parts, recognizing the importance of creating an environment that prioritizes the well-being of drivers and passengers.
In response to evolving customer requirements for enhanced scratch resistance, Xiangxichem took a step further in product development. Ultra-high molecular weight silicone scratch-resistant agents, containing special functional groups, were introduced. This ongoing phase of research and development is characterized by a commitment not only to meeting existing demands but also pushing the boundaries of performance.
The ultra-high molecular weight silicone scratch-resistant agents represent a new frontier, incorporating special functional groups to elevate scratch resistance to an unparalleled level. This addresses the evolving needs of customers who seek not only basic scratch resistance but a superior level of protection for PP interior materials.
In conclusion, the developmental journey of XiangxichemDX8502 reflects a commitment to innovation and a dynamic response to the changing landscape of automotive interior material requirements. From pioneering efforts to address fundamental scratch resistance to ongoing advancements that push the boundaries of performance, Xiangxichem’s scratch-resistant agent stands as a testament to the pursuit of excellence in creating a more comfortable, beautiful, and safe car interior environment.
Through the anchoring effect in the resin, it has good compatibility with PP materials. Compared with ordinary silicone types, it is easier to be evenly concentrated on the surface of the material. It has a quick effect and gives PP materials excellent scratch resistance at low addition amounts. It has excellent scratch-wiping performance, and at the same time, it will not appear sticky and yellowing after being exposed to high-temperature light. It can also effectively avoid the stress whitening problem caused by adding anti-scratch agents. Due to the characteristics of the product itself, it improves the air quality inside the car from the source and is more environmentally friendly and safe.
Stage Two: Advancements in Performance (Ongoing)
In the dynamic period spanning from 2020 to 2022, consumer consciousness has pivoted significantly towards the air quality within the confines of their cars. This heightened awareness has prompted the automotive industry to place paramount importance on the measurement of Volatile Organic Compounds (VOCs). Customers, in turn, are now expressing stringent requirements for minimizing odors, and this collective concern has catalyzed a transformative phase in the realm of scratch-resistant agents for automotive Polypropylene (PP).
This critical juncture in the industry has necessitated a reevaluation and enhancement of odor control strategies within scratch-resistant agents, marking a breakthrough in addressing air quality concerns. To meet this challenge head-on, comprehensive measures have been implemented to usher in a new era of odor improvement.
One of the key initiatives involves the integration of new production equipment and post-processing facilities. This technological upgrade is instrumental in ensuring that scratch-resistant agents undergo a thorough and meticulous treatment, effectively minimizing any residual odors. The addition of advanced equipment aligns with the industry’s commitment to providing consumers with not just scratch-resistant solutions but also a superior olfactory experience within their vehicles.
In tandem with technological upgrades, there has been a significant increase in the frequency of odor testing. Outgoing products are subjected to rigorous assessments, and only those meeting stringent standards are cleared for distribution. This heightened scrutiny ensures that the scratch-resistant agents not only excel in performance but also contribute to an overall improvement in the air quality within cars. It’s a proactive step towards aligning with consumer expectations and industry standards.
The focus on quality control extends beyond the final product to the very roots of the manufacturing process—the raw materials. Stringent measures have been put in place to ensure the quality of raw materials, encompassing an expanded array of testing items and an increased testing frequency. By addressing odor control at the source, manufacturers are taking a preventive approach to ensure that the scratch-resistant agents are not just effective but also contribute to a fresher in-car environment.
Recognizing the integral role of personnel in this process, a pivotal step has been quality awareness training for production personnel. This training is designed to instill a heightened sense of quality consciousness among those involved in the manufacturing process. By fostering a culture of quality awareness, every individual becomes a stakeholder in the mission to deliver scratch-resistant agents that not only meet but exceed customer expectations.
This multifaceted approach to odor improvement in automotive PP scratch-resistant agents represents a paradigm shift in the industry’s response to consumer demands. It goes beyond the traditional focus on performance and durability to address the holistic in-car experience. As consumers become increasingly discerning about the air they breathe within their vehicles, this commitment to odor control becomes a pivotal factor in the overall satisfaction and well-being of drivers and passengers.
industry’s response to the evolving landscape of consumer preferences reflects a dedication to innovation and a proactive stance in addressing emerging concerns. The integration of advanced equipment, stringent testing protocols, quality control measures, and personnel training collectively represent a holistic strategy to usher in a new era of scratch-resistant agents—one that not only excels in performance but also elevates the in-car environment to unprecedented levels of comfort and freshness.
Since 2019, we’ve worked together to raise the bar for odor control in automotive polypropylene (PP) anti-scratch compounds. This initiative is marked by the establishment of a dedicated team of professional quality testers whose primary focus is to comprehensively evaluate and enhance the olfactory experience associated with our products.
A key component of this quality assurance strategy is the careful selection and organization of the odor assessment team. Members of the team are subject to a strict set of guidelines that emphasize the importance of maintaining best practices to ensure fair and accurate evaluations. These guidelines include avoiding smoking, drinking alcohol, eating spicy foods and using cosmetics. By adhering to these standards, the team ensures that their sensory perceptions remain intact, providing a reliable basis for odor assessment. Test conditions have been significantly upgraded to create an environment conducive to accurate evaluation. This includes providing a dedicated testing location with consistent temperature and humidity levels, free from disturbances and external odors. The aim is to create an environment in which the olfactory properties of anti-scratch agents can be assessed with focus and accuracy.
Recognizing the dynamic nature of the field, members of the odor assessment team regularly participate in professional odor testing training. These training sessions are designed to improve their olfactory acuity and keep them abreast of the latest developments in odor assessment methods. This commitment to continuous improvement ensures the team remains at the forefront of odor assessment, contributing to the overall enhancement of our scratch-resistant agents. To establish a baseline for odor assessment, the team organized visits to client companies. During these visits, the team works with the client’s testing team to conduct scent testing benchmarks. This collaborative approach not only facilitates the exchange of knowledge but also ensures that our anti-scratch agents meet our customers’ specific odor expectations. This is a proactive move to meet diverse customer needs and improve the overall quality of our products.
When it comes to interior variety, the industry recognizes that no two vehicle interiors are the same. This realization prompted a paradigm shift in scratch resistance testing methods. From early days when only smooth surfaces were tested, the current situation involves comprehensive scratch resistance testing covering both rough and fine skin textures. This adaptability is essential to meet the different needs of different interior designs.
Advances in testing methods have paralleled developments in interior design. The instrumentation used in scratch resistance testing not only keeps pace with industry advancements, but also drives advancements by introducing more comprehensive testing methods and types. The evolution from testing black interiors to adapting to lighter-colored interiors with higher scratch-resistant requirements is evident.
Multiple advances in instrumentation and test methods underscore the commitment to staying ahead of the curve. As automotive interiors continue to diversify, the industry’s scratch resistance testing methods remain flexible and adaptable. The ability to test rough and fine skin textures and meet different color requirements demonstrates the industry’s commitment to delivering scratch-resistant agents that meet the ever-changing needs of automakers and, ultimately, consumers.
Initiatives taken since 2019, including the establishment of a specialist quality testing team and an ongoing commitment to improving odor assessment, represent a holistic approach to ensuring that scratch-resistant agents meet the highest standards. The industry’s response to the diversity of automotive interiors is reflected in the development of scratch resistance testing, further cementing its commitment to innovation and meeting the ever-changing needs of the automotive industry.
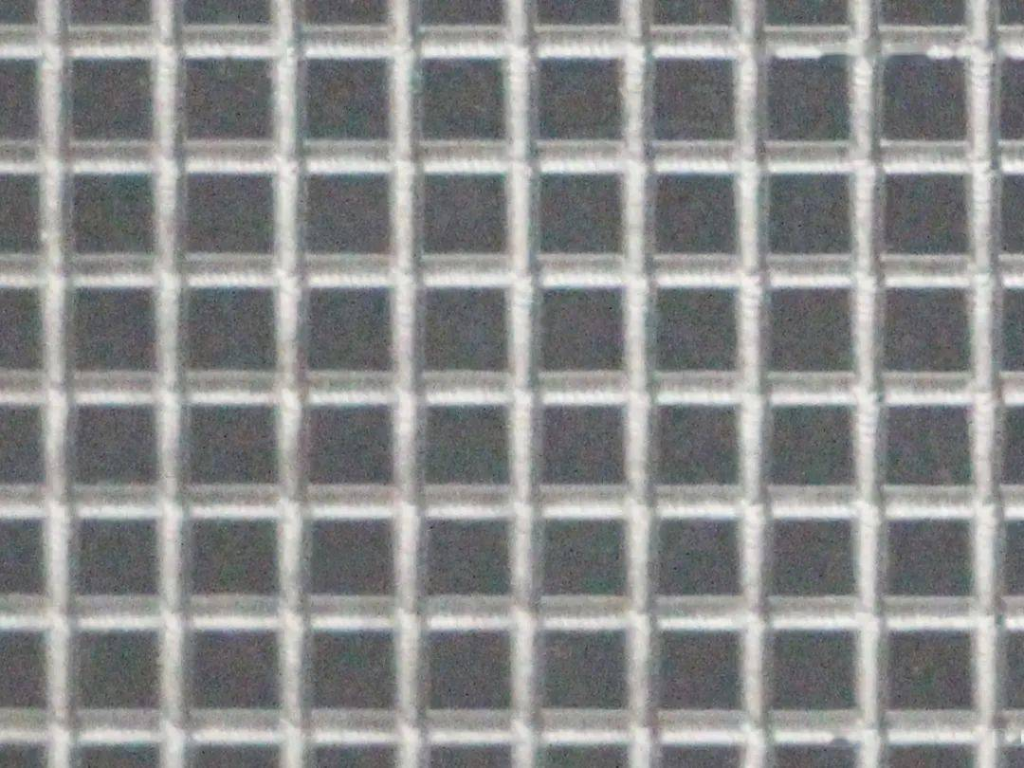
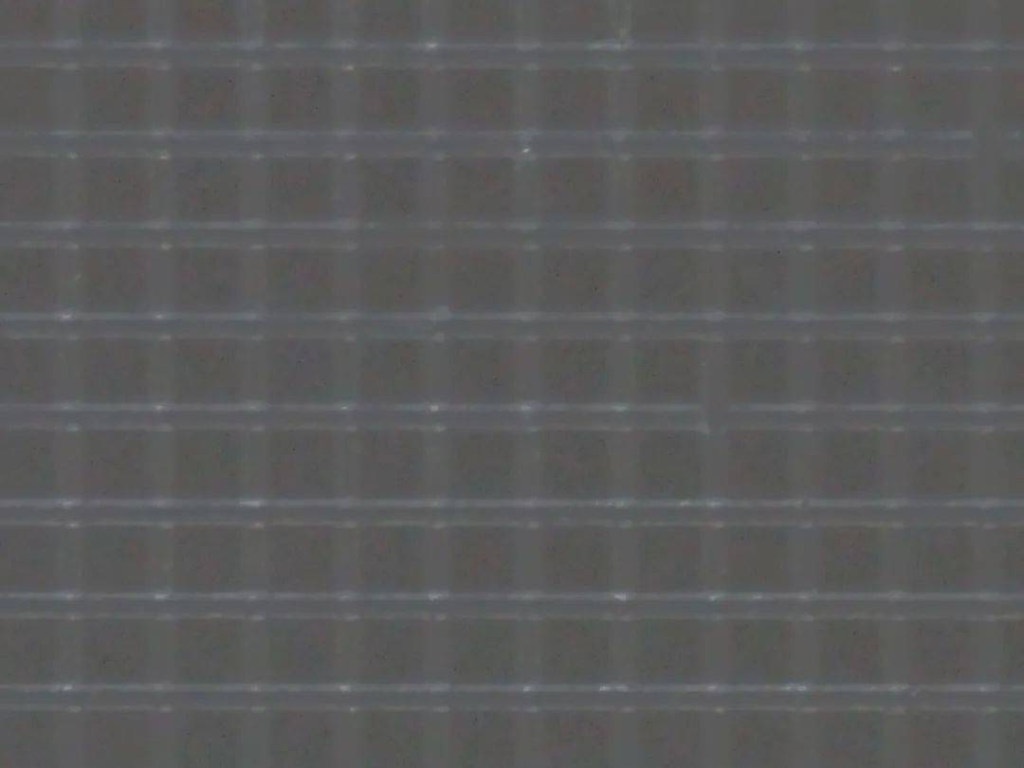
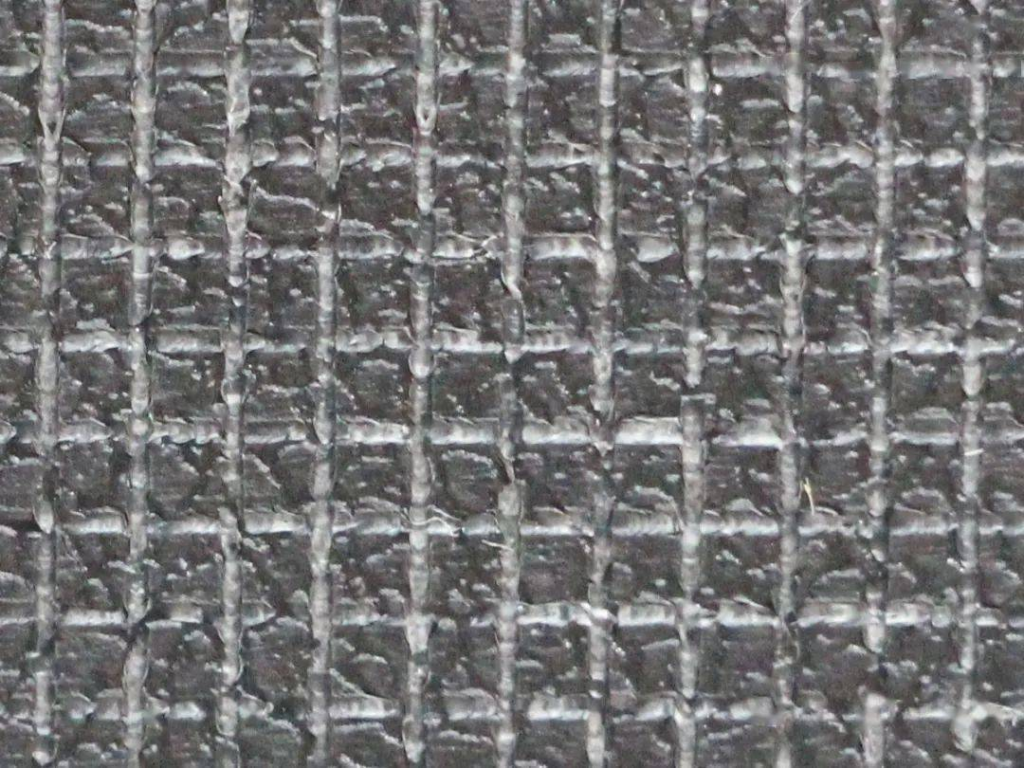
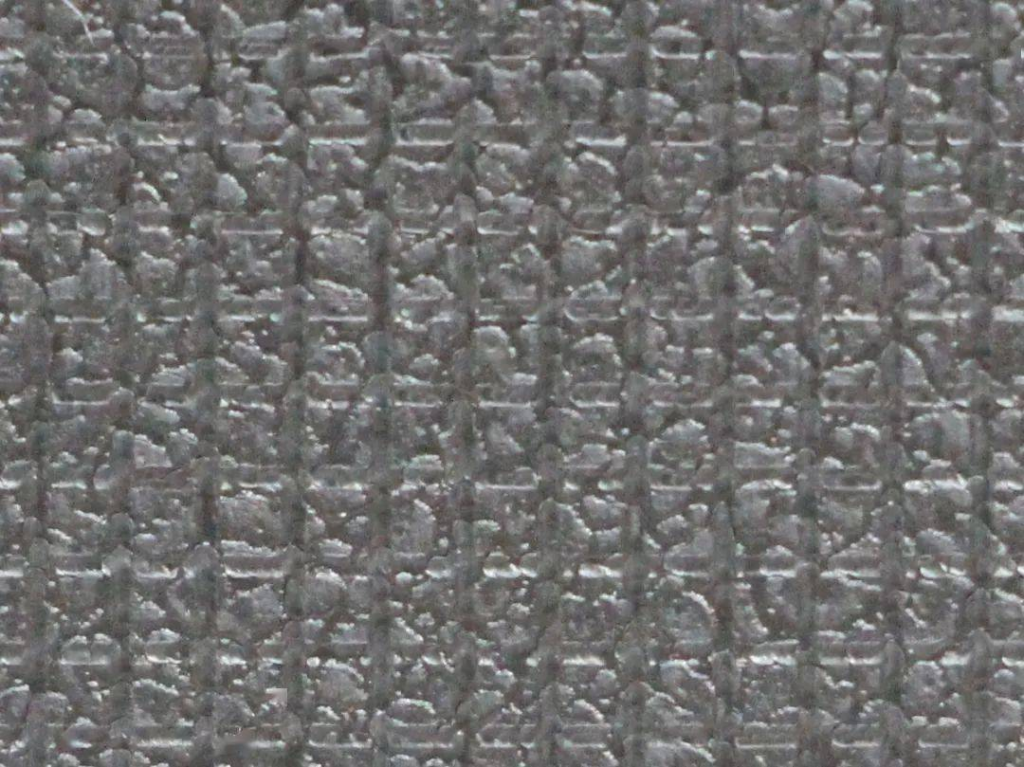
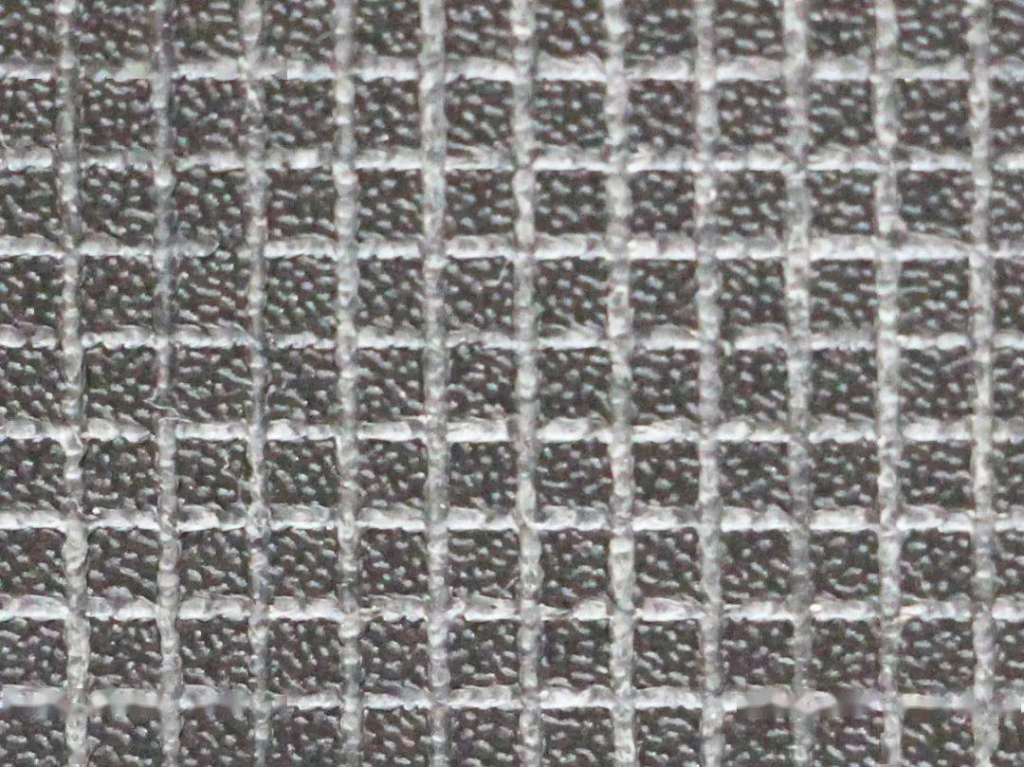
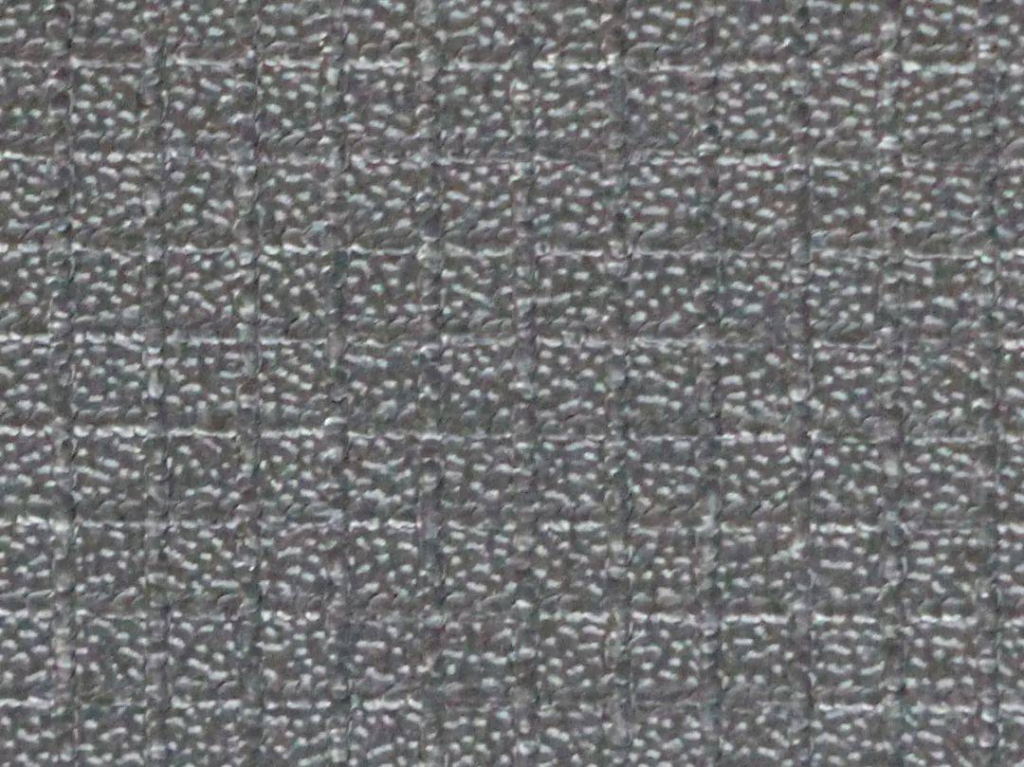
As highlighted before, the scratch resistance requirements for light-colored interiors also increase. Meeting this demand presents a dual challenge, requiring a delicate balance between achieving optimal scratch resistance and mitigating adverse effects. One approach is to increase the amount of anti-scratch agent added; however, this approach carries the risk of flow marks and bright spots, which are undesirable consequences of common ultra-high molecular weight silicones.
The challenge is twofold: on the one hand, it is necessary to meet the higher scratch resistance requirements of light-coloured interiors and, on the other hand, to prevent run marks and bright spots from appearing, which could impair the visual appeal. Internal components. An important realization in this process is that traditional ultra-high molecular weight silicones, while effective in enhancing scratch resistance, may inadvertently introduce visual defects.
One way to address this challenge is through silicone modification. This requires a nuanced approach to modifying the properties of the silicones used in anti-scratch agents, aiming to achieve a harmonious balance between scratch resistance and visual aesthetics. Silicone modification offers the possibility to tailor the performance characteristics of the anti-scratch agent, ensuring that it not only meets the demanding requirements of light-colored interiors but also maintains the pristine appearance expected by consumers. The process of solving this dual challenge involves a strategic examination of the molecular structure of silicones. By introducing modifications, scratch resistance can be enhanced without affecting the visual effect. The result is a scratch-resistant agent that not only meets the specific needs of light-colored interiors, but also provides a seamless and visually appealing finish.
It is important to realize that the pursuit of optimal scratch resistance is a complex process between meeting functional requirements and maintaining the aesthetic integrity of the vehicle interior. The decision to go with silicone modifications reflects our commitment to delivering scratch-resistant agents that go beyond functionality – they embody a holistic approach that takes into account the visual nuances critical to customer satisfaction. The industry’s response to higher scratch resistance requirements for light-coloured interiors is not a one-size-fits-all solution. Rather, it involves a strategic interplay of factors, where the amount added is weighed against potential visual drawbacks. The introduction of silicone modification represents a sophisticated approach to achieving the delicate balance required for scratch resistance in light-colored interiors, acknowledging that the pursuit of excellence extends beyond mere functionality to encompass the visual aspects of automotive interiors. attraction.
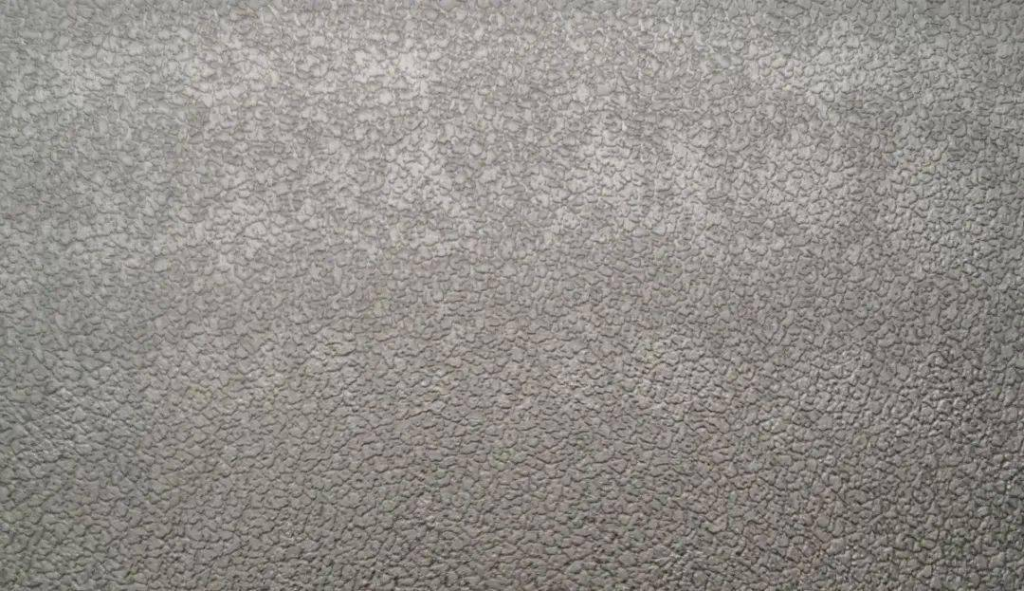
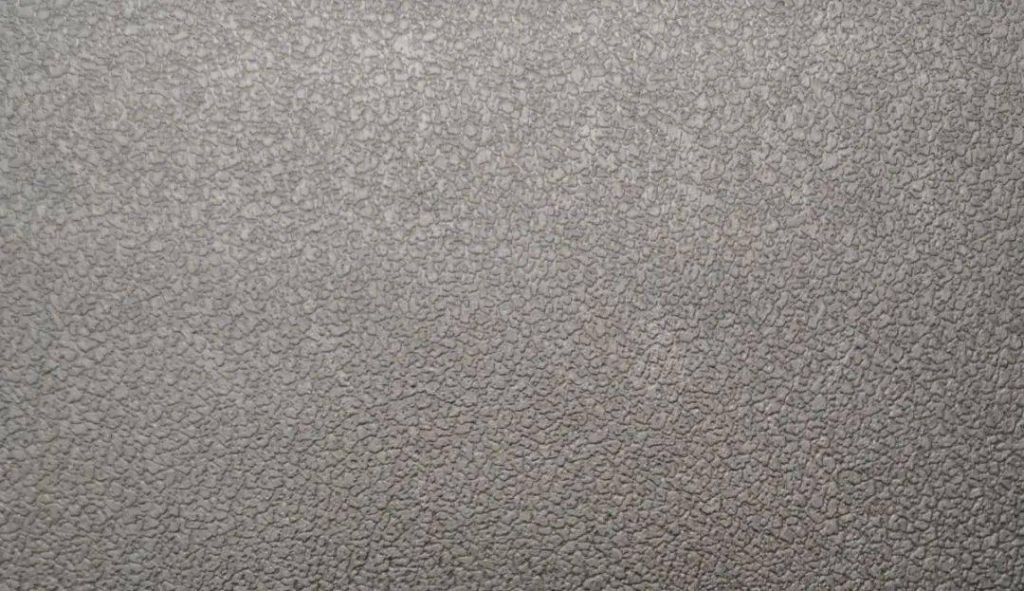
In order to meet the higher scratch resistance requirements of light-colored interiors, we have specially developed an PP scratch resistant agent that not only has excellent scratch resistance, but also solves the phenomenon of flow marks. This strategic development is part of an ongoing process that involves meticulous tuning and the creation of samples, all with the goal of improving the anti-scratch compound to meet and exceed industry expectations.
The research and development process is like a wheel that is always moving forward, and its power comes from the product itself. This ongoing cycle is characterized by an unwavering commitment to achieving breakthroughs in the performance of PP scratch resistant agent and exploring new frontiers of functionality and technology. The aim is not just to keep up with industry demands, but to lead the way and ensure that anti-scratch agents continue to evolve to meet the ever-changing needs of the automotive industry.
A key aspect of this evolution is the incorporation of silicone modifications. This nuanced approach is not just a technology, but a transformative approach to redefining the performance characteristics of PP scratch resistant agent. Silicone modification becomes a catalyst for enhanced scratch resistance while solving challenges such as flow marks. It represents a dynamic and responsive strategy that can be customized to enhance, ensuring that the anti-scratch agent is not only effective but also versatile to meet different requirements.
With adjustments and sample iterations ongoing, every stage of the R&D process is guided by an unwavering commitment to excellence. Our goal was to create a PP scratch resistant agent that not only meets the strict standards set by light-colored interiors, but also exceeds expectations by mitigating the visual imperfections associated with traditional methods.
Looking to the future, Xiangxi Chemical will increase its efforts to develop more differentiated anti-scratch agents for automotive polypropylene (PP) interior materials. This forward-looking commitment is based on the understanding that future needs will continue to evolve and diversify. Through continuous research and development, Xiangxi Chemical is committed to being at the forefront of innovation, ensuring that the PP scratch resistant agent it provides not only meet current needs, but can also meet future challenges and opportunities.
Finally, the journey to develop advanced anti-scratch agents is emblematic of the dynamic nature of the industry and Xiangxi Chemical’s strong commitment to innovation. Through the strategic application of silicone modifications and an unwavering commitment to excellence, the company is committed to shaping the future of scratch-resistant additives for automotive PP interior materials, meeting and exceeding the diverse and ever-changing needs of the automotive industry.
This topic will continue from xiangxichem guide